What Are the Different Types of Automotive Fuel Injection?
Throttle Body Injection vs. Multi-Port Injection vs. Direct Injection
To put it simply, your engine combusts a mixture of fuel and air inside its cylinders to move the pistons that create the forward or backward motion that's eventually transferred to the wheels. How the fuel gets to the cylinders, when the fuel gets there, and how the fuel is used are some of the most important factors in determining your engine's power and efficiency.
Older engines used a carburetor to meter fuel to the engine. In carbureted engines, the incoming air in the intake would create a vacuum that pulled fuel out of a tube in the carburetor called a venturi. This system was relatively simple and easy to work on, and was successful for many years. Eventually fuel injection was found to be more efficient. Fuel injected engines could produce more power, use less fuel, and more easily pass increasingly strict emissions standards. Today, all new cars use some form of fuel injection.
Various methods of injecting fuel into the engine have been developed over time. These can be split into categories based on where the fuel is added. Over time, the point of injection has moved closer and closer to the cylinders themselves. The three major types of fuel injection are known as throttle body injection, multiport injection, and direct injection. We'll walk you through the three types, explain how each one works, and describe the advantages and disadvantages of each type.
Throttle Body Injection
Throttle body injection (TBI), also called single point injection was the first type of fuel injection widely in use in cars. It worked very similarly to a carburetor in that it metered out fuel into the front of the intake manifold, behind the throttle body. The fuel and air mix in the intake manifold and are drawn into the cylinders by the suction produced during each cylinder's intake stroke.
Throttle body injection was a big improvement over carburetion. The vehicles onboard computer, the engine control unit (ECU), could control the amount of fuel metered out and the timing of the fuel. That makes TBI more efficient than carburetion over a wider range of operating conditions.
TBI had certain problems in common with carburetion, though. First, since the fuel has to travel a relatively long distance to the cylinders it can condense and pool in the intake manifold. Cylinders closer to the throttle body might also receive a richer mix of fuel and air, compared to those cylinders farther away, which receive a leaner mix.
Although TBI did have the advantage of being simple by having only one or sometimes two injectors, it was eventually phased out in favor of multi-port injection.
Multi-Port Injection
Multi-port injection (sometimes called multi-point injection) uses separate injectors to spray fuel into each cylinder. The injectors are mounted into the intake ports, just outside each cylinders intake valve. Two types of central port injection have been used and sequential multi-port injection.
In central port injection, a central fuel unit sends fuel down a series of legs which end in poppet valves. The look of this type of injector led some people to refer to it as a spider injector. All the valves release their fuel at the same time, which means some of the fuel is left waiting until the next intake stroke. That allows the fuel a chance to condense, which means it won't combust as readily.
Sequentially fuel injection solves this problem, by having each injector valve open up in time with its corresponding intake valve. The injector timing is controlled by the ECU much like ignition spark timing.
Central port injection is more efficient than TBI, and sequential multi-port injection is more efficient too. Each of those systems, though is more complicated, with more moving parts, which makes them harder to work on and more expensive to build. That being said, sequential multi-port injection is the most common fuel metering system in gas-powered cars today.
Direct Injection
In direct injection systems, fuel is injected directly into the cylinder. That makes for the best mix of fuel and air. Direct injection has been used in diesel engines since the 1920s and in gasoline powered aircraft engines since around World War II, but has only seen much recent use in gas powered cars. Performance auto makers like Audi and BMW have discovered that the more efficient combustion in gasoline direct injection (GDI) helps produce more powerful engines. Some automakers have also started using GDI to make engines use less gas. GM's Ecotec and Ford's Ecoboost engines both use GDI.
GDI engines can use very lean fuel-air mixes when the engine is under light load. This helps save gas, but it creates nitrous oxide emissions. GDI engines rely on exhaust gas recirculation and specially designed catalytic converters to clean up these emissions. GDI systems also need sturdier injectors. The injectors are exposed to the heat and pressure of the combustion chamber, and the injector has to spray against the high pressure of combustion chamber. While normal fuel injectors spray out gasoline at 40 to 60 pounds per square inch, direct injectors have to spray the fuel at thousands of psi.
So, while direct injection is the best option in terms of power and efficiency, it is also the most complicated and expensive system.
As technology advances, direct injection engines may become easier to manufacture, but, for now, sequential multi-port injection remains the most common fuel injection system in cars today. It provides the right mix of efficiency and affordability for most applications.
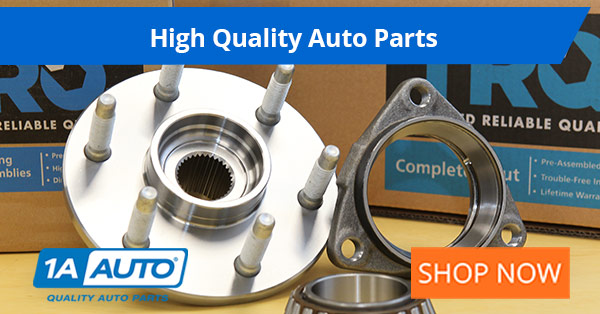